For many years shipping containers have been repurposed for various applications such as storage units, retail and temporary housing solutions and health care facilities. Since containers are highly versatile this makes them an ideal choice for many innovative projects.
Shipping containers were originally designed for transportation, but over the years, they have been repurposed for various applications. The ability to transform and repurpose shipping containers have become symbols of sustainability and resourcefulness in modern architecture and design. Because shipping containers are highly durable, cost-effective which reduces energy usage and eco-friendly, many are transformed by customizing or complete re-build.
Jump to:
- Planning and Designing Your Custom Container
- Customization Ideas and Inspirations
- Structural Modifications and Considerations
- Utility Installations
- Legal and Safety Regulations
- Finding the Right Contractors and Suppliers
- Cost Analysis and Budgeting
- Maintenance and Upkeep
- How to Avoid Shipping Container Scams
Planning and Designing Your Custom Container
When you decide to customize or rebuild a shipping container it is important to consider purpose, size, location, budget. Your purpose is to determine if the modifications or rebuild you are considering is suitable for the end result of what you want. For example, if you plan to use the shipping container as an office, you will need to include windows, doors insulation and other amenities. The purpose of the container will also determine the size and type required. Shipping containers come in various sizes, including 10 ft., 20ft and 40ft in length. For example, if you are making a retail pop up store you may not need a large shipping container. Also, you may consider an Open Sided container when designing a restaurant or bar.
Another thing to think about is the location of where you need the shipping container. It is important to ensure that the container is placed in an optimal location that has good terrain and accessibility. Remember if you place the container in a residential area, you may need to obtain permits and comply with your local zoning laws.
Finally, your budget will depend on the extent of the modifications or rebuild based on the cost and the materials used. A qualified welder, contractor or fabricator can help you design and implement the conversion of your project safely and to code. According to Angi, the average cost to build a shipping container home is $ 30,000. And according to Boxman Studios, the cost to build out a kitchen can range from $ 180,000 to $300,000 for a 600 sq.ft space. However, the total cost can be higher if you attach multiple containers together to make a larger space. Does not include the cost of land, permits and other miscellaneous expenses.
Despite everything, shipping container architecture remains a popular and growing trend in the world of design.
There are many tips for maximizing space and functionality. First, plan ahead. Have a clear idea of what you want to achieve. Maximize the shipping container vertical floor space by using multifunctional furniture that serves more than one purpose. Especially when building a shipping container home, office, or retail. Use natural light by adding windows or skylights.
Customization Ideas and Inspirations
Many residential, business and industries use shipping containers beyond just for storage. Customized shipping containers often present an attractive display or exhibit of your home, business or retail as offices, pop-up shops, studios and more. You can visit our website for 26 of our favortie shipping container ideas. To get your started, here are some of the most common uses for shipping containers:
Home Building
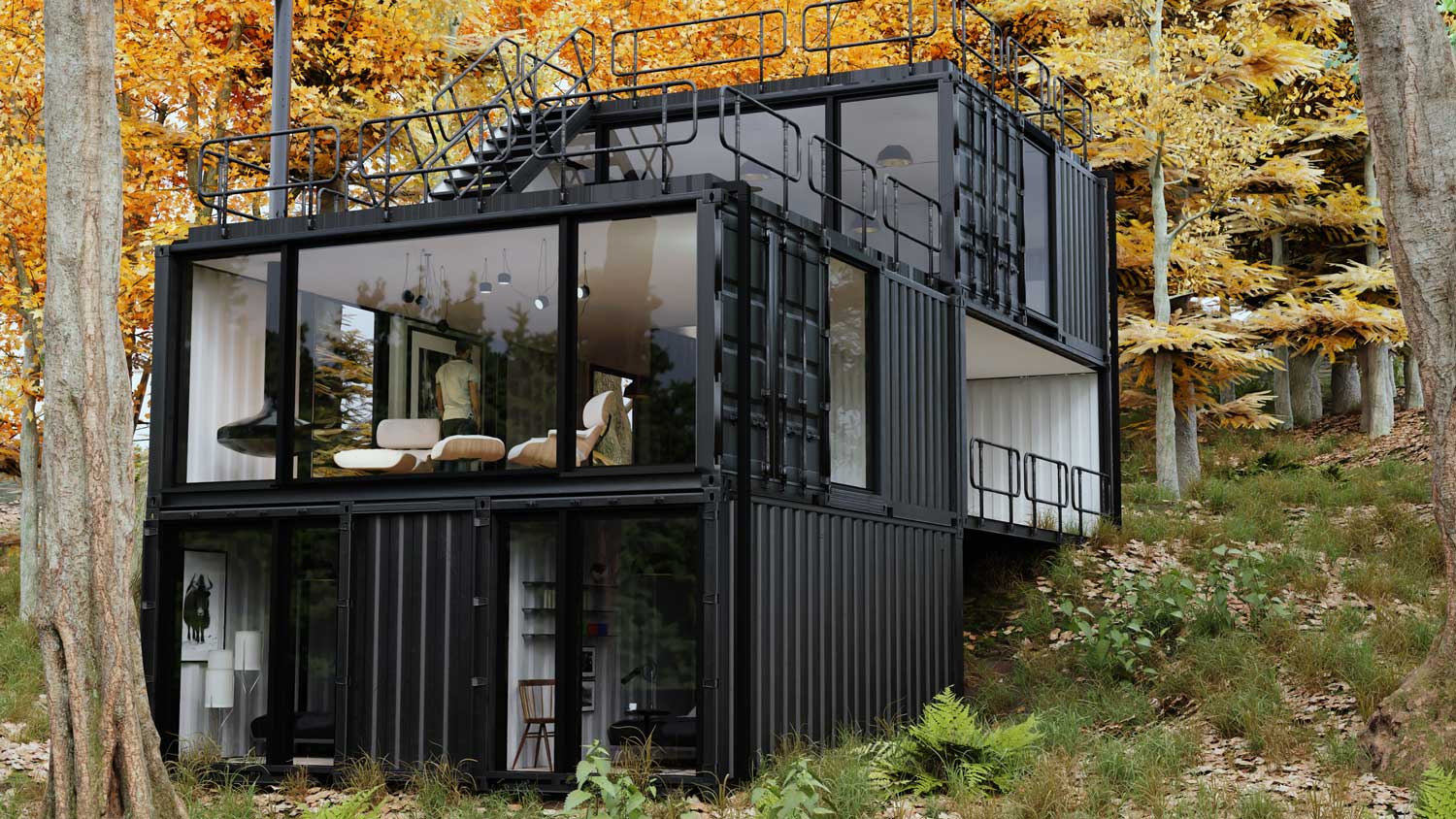
Restaurant / Retail / Café
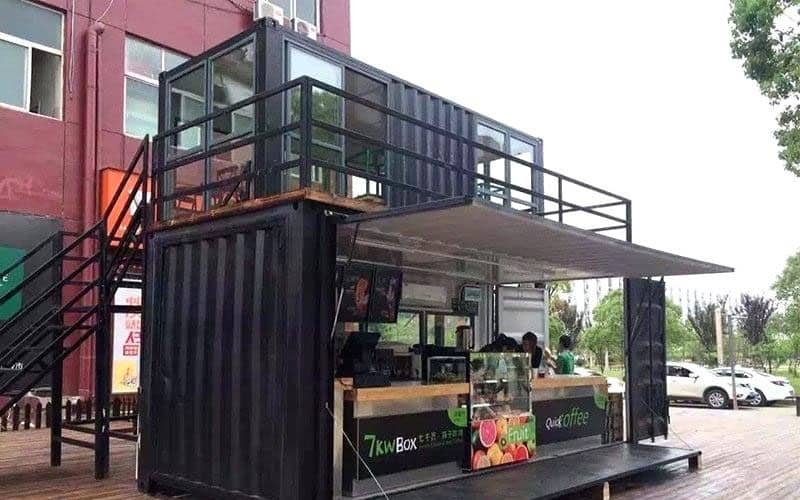
Hotel
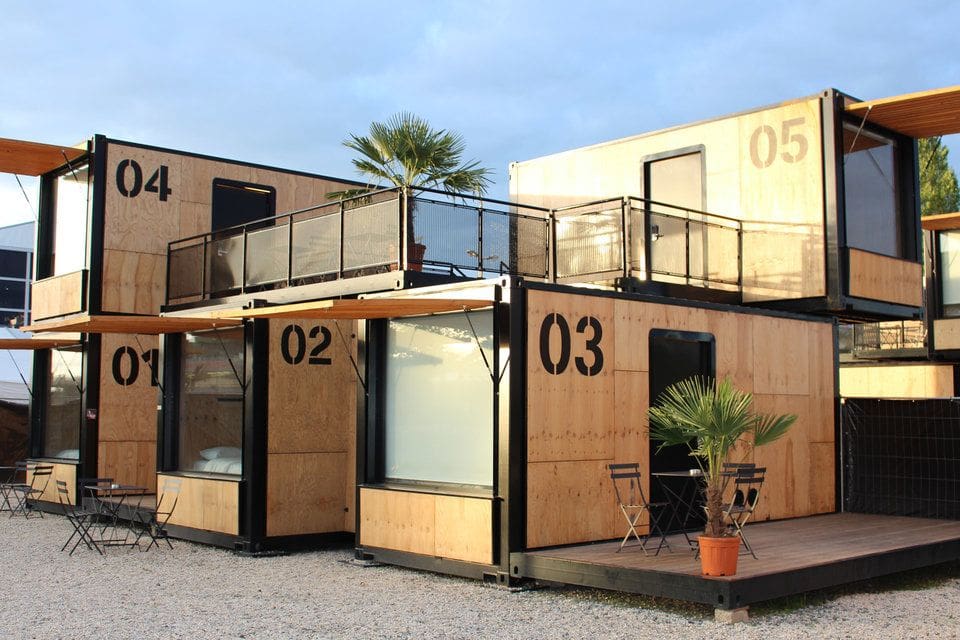
Schools / Universities
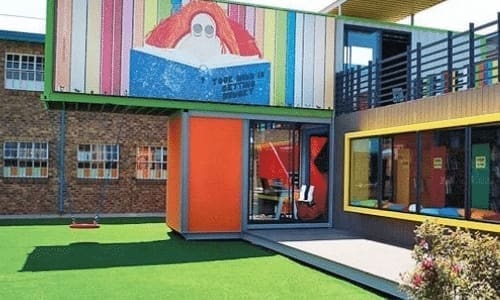
Offices
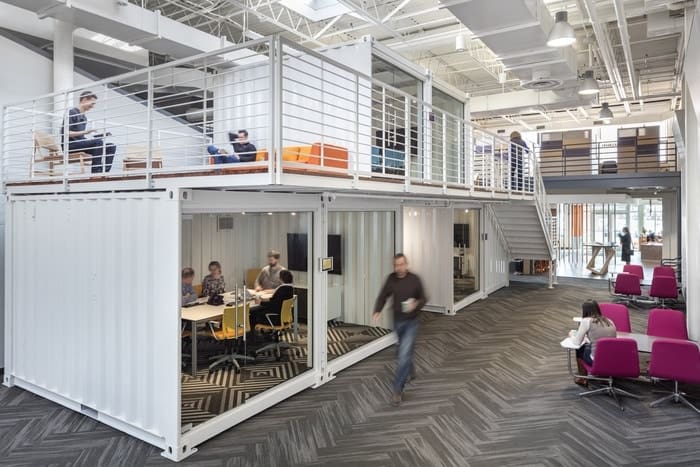
Portable Toilets
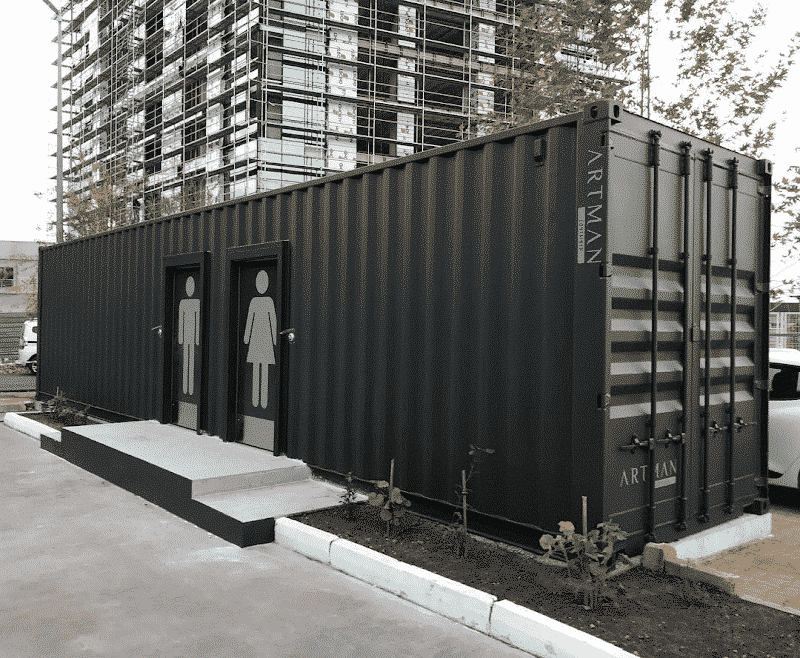
Workshops
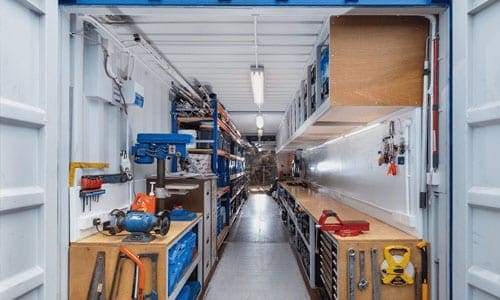
Fire & Police departments
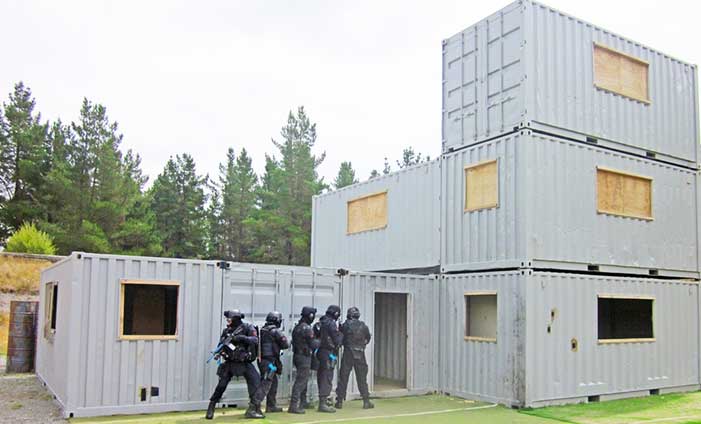
Medical Facilities / Hospitals
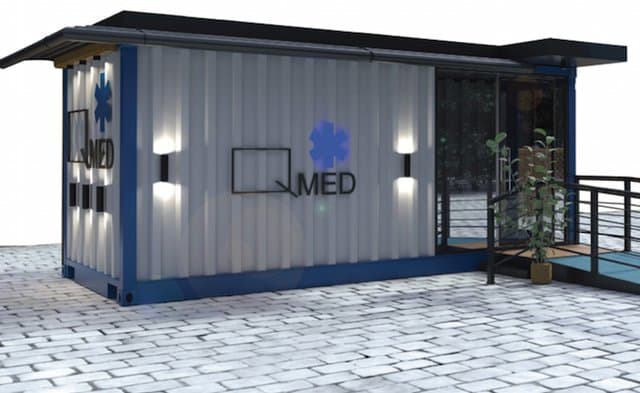
Structural Modifications and Considerations
When cutting or modifying the walls of a shipping container to install windows, doors, mounted air/ heat units, skylights, etc., it’s important to make sure that the structural integrity of the container is not jeopardized. Too many alterations or cutting out an entire wall may cause the roof to sag or the structural integrity to give. It is best to consult with a professional contractor, welder or fabricator who can provide expert advice on this matter.
Shipping containers are made from Corten Steel, which can create a considerable amount of condensation and heat in some areas in the summer. There are several types of insulation materials available for shipping containers, including blanket insulation, spray foam, glass wool blanket insulation, expandable foam, traditional roll, loose-fill, cork, and denim insulation. The best type depends on climate & location. Generally, a high R-Value spray foam and fiberglass panels are typically the most popular and effective for most shipping containers.
Other ways to provide climate control in a shipping container:
- Place the container in shade to reduce the amount of direct sunlight it receives.
- Paint the roof and exterior side walls with white reflective or light gray paint.
- Install extra Ventilation, like fixed, louvered and rooftop turbines.
- Arrange items to facilitate airflow.
- Installing a solar panel on your shipping container roof can help power a fan or air conditioning unit.
Utility Installations
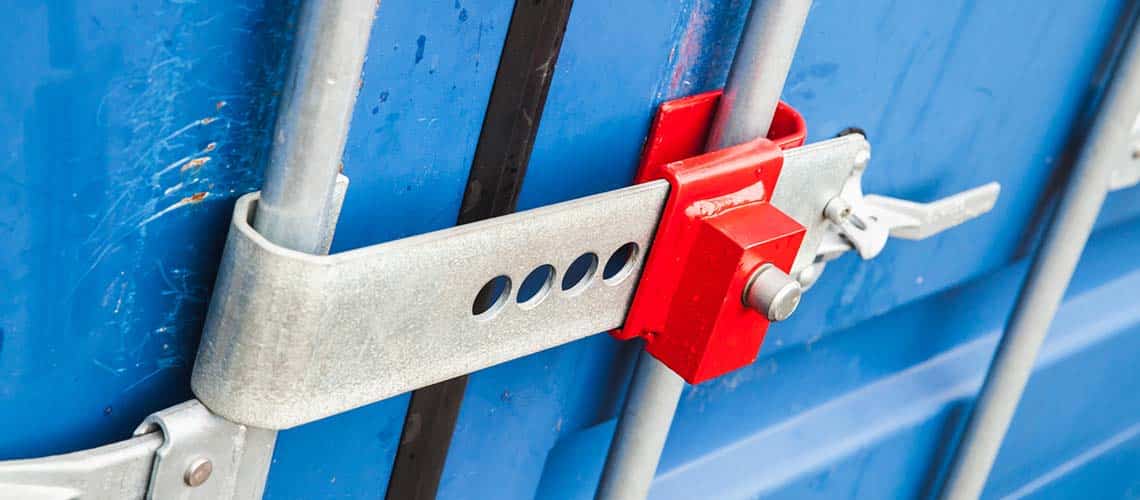
Transforming a shipping container into a functional space involves various fabrication options, depending on the intended use. Here are some common fabrication options you can consider.
- Windows and Doors: Adding windows and doors is essential for natural light and access. You can choose from different sizes and styles, including sliding glass doors, roll-up doors, or standard residential doors.
- Insulation: To make the container habitable, especially in extreme climates, insulation is crucial. Options include spray foam, panel insulation, or blanket insulation.
- Electrical and Plumbing: a livable or functional space, you’ll need to install electrical wiring and plumbing. This includes outlets, lighting, and plumbing for bathrooms or kitchens.
- HVAC Systems: Heating, ventilation, and air conditioning systems are important for maintaining a comfortable temperature inside the container.
- Interior Walls and Flooring: Adding interior walls can create separate rooms or areas. Flooring options range from basic plywood to laminate, hardwood, or even tile.
- Roofing Modifications: Some projects may require modifications to the roof, such as adding a pitched roof, skylights, or a rooftop deck.
- Exterior Finishes: You can paint the exterior, add cladding, or use other materials to improve the container’s appearance and protect it from the elements.
- Security Enhancements: Consider adding security features like locks, alarm systems, or reinforced doors and windows for added safety.
- Custom Features: Depending on the use, you might add custom features like built-in furniture, shelving, or specific equipment for an office, workshop, or studio.
- Structural Modifications: For larger spaces, containers can be cut and combined. Structural reinforcements might be needed when removing sections of the container for larger openings or stacking containers.
When considering sustainable options for fabricating shipping containers, several innovative approaches can also be explored:
- Recycled Materials: Using recycled steel or aluminum reduces the carbon footprint associated with new material production. Recycled plastics can also be incorporated into components.
- Wooden Containers: Using sustainably sourced wood for container construction can be an eco-friendly alternative, especially if it comes from certified managed forests. However, durability and strength need to be considered.
- Eco-friendly Coatings: Traditional paints and coatings can be toxic. Using eco-friendly, low-VOC (Volatile Organic Compounds) paints and protective coatings can minimize environmental harm.
- Solar Panels: Incorporating solar panels into container designs could help in powering onboard systems or contributing to the energy needs of the transport vehicle.
- Improved Insulation: Using advanced insulation materials can improve temperature regulation inside containers, making them more energy-efficient for transporting temperature-sensitive goods.
It is best to work with your builder or contractor to discuss the advantages and challenges of each approach.
Ready to purchase a shipping container? Reach out today to get a quote from the best in the industry!
Legal and Safety Regulations
Customizing a shipping container for use as a living space, office, or other functional structure involves several considerations regarding building codes and permits. These regulations can vary widely depending on the location, but here are some general aspects to consider:
- Zoning Laws: Before beginning any project, check local zoning laws to ensure that shipping container homes or structures are permitted in the desired area. Zoning laws dictate what kind of structures can be built in specific areas.
- Building Codes: Adhering to local building codes is essential. These codes cover aspects like structural integrity, electrical wiring, plumbing, ventilation, and insulation. Shipping container modifications often need to comply with the same standards as traditional construction.
- Permits: Most locations require building permits for constructing or significantly modifying a shipping container for use as a dwelling or functional building. The process involves submitting plans for approval and undergoing inspections during and after construction.
- Foundation Requirements: Like traditional buildings, shipping container structures usually need a foundation, which must comply with local codes for stability and safety.
- Insulation and Ventilation: Proper insulation and ventilation are crucial for making the container habitable, especially in extreme climates.
- Electrical and Plumbing: If the container will have electricity and plumbing, these systems must meet local codes for safety and functionality.
- Egress and Accessibility: Codes often require a certain number of exits and may have specific requirements for accessibility, especially if the container is used for commercial purposes or public use.
- Height and Size Restrictions: There may be limitations on how tall or large your container structure can be. This is often dictated by local building codes and zoning laws.
- Fire Safety: Fire safety regulations, including the use of fire-resistant materials and the installation of smoke detectors, are crucial components of building codes.
- Environmental Regulations: Some areas have regulations related to environmental impact, such as rainwater runoff, waste management, and energy efficiency.
It’s essential to consult with local building authorities, hire knowledgeable contractors, and potentially involve an architect or engineer who is familiar with the unique aspects of shipping container construction. Understanding and complying with these regulations is critical to ensuring the safety, legality, and success of your project.
Finding the Right Contractors and Suppliers
Finding the right contractors for customizing a shipping container is a critical step in ensuring the success of your project. Here are the steps to finding a good fit:
- The first step is to look for contractors who specialize in shipping container modifications. Experience in this specific field is crucial as it requires unique skills and knowledge compared to traditional construction.
- Conduct interviews to get a sense of their communication style and response time. Also, ask potential contractors for a portfolio of their previous work, specifically with shipping containers.
- The contractor should be familiar with local building codes and permit requirements related to shipping container customization. This knowledge is crucial for a hassle-free project.
- Ensure that the contractor you select is licensed and insured. This protects you from liability in case of accidents or damage during the project.
- Finally, before signing a contract, make sure you understand all its terms, including the scope of work, timeline, payment schedule, and provisions for handling changes or unforeseen issues.
By carefully selecting a contractor who is experienced, reliable, and communicative, you can ensure that your shipping container customization project is completed successfully, meets your expectations, and complies with all necessary regulations.
Ready to purchase a shipping container? Reach out today to get a quote from the best in the industry!
Cost Analysis and Budgeting
The cost of modifying a shipping container can vary widely depending on several factors like the type of modification, the quality of materials used, the location, and the cost of labor. Here are rough cost estimates for various types of modifications:
Basic Modifications
- Windows and Doors: Adding basic windows and doors can range from $1,000 to $4,000, depending on the size and quality.
- Insulation: Insulating a container might cost between $1,500 and $5,000, depending on the insulation type and container size.
- Basic Electrical and Plumbing: Simple electrical and plumbing work can range from $1,000 to $10,000, varying greatly based on complexity and local code requirements.
Full Home Conversion
- Standard Home Features: Converting a container into a livable home with features like a kitchen, bathroom, living area, and bedroom can range from $20,000 to $50,000 or more.
- HVAC Systems: Installing heating, ventilation, and air conditioning systems can add $3,000 to $10,000.
Office or Workshop Conversion
- Basic Office Setup: A simple office setup with electrical wiring, lighting, and basic furnishings can start from $10,000 to $25,000.
- Advanced Workshop: More sophisticated modifications for a workshop with heavy-duty electrical systems and custom fittings can range from $20,000 to $40,000.
Commercial Spaces (Cafes, Retail Stores, etc.)
- Basic Retail Space: A simple conversion for a small retail space may cost between $15,000 and $30,000.
- Custom Commercial Space: For more elaborate designs and customizations, costs can exceed $50,000.
Eco-Friendly Modifications
- Solar Panels: Adding a solar power system can range from $5,000 to $20,000, depending on the system size and capacity.
- Green Roofing: Installing a green roof for better insulation and aesthetics can add $10,000 to $25,000.
Exterior Modifications
- Paint and External Finishes: Professional painting and external finishes can range from $2,000 to $10,000.
- Decking and External Structures: Adding external structures like decks or awnings can cost $5,000 to $20,000.
Remember, these are rough estimates and actual costs can vary significantly based on local prices, the specific needs of the project, the condition of the container, and the complexity of the work required. It’s always a good idea to get multiple quotes from contractors to get a more accurate estimate for your specific project.
Maintenance and Upkeep
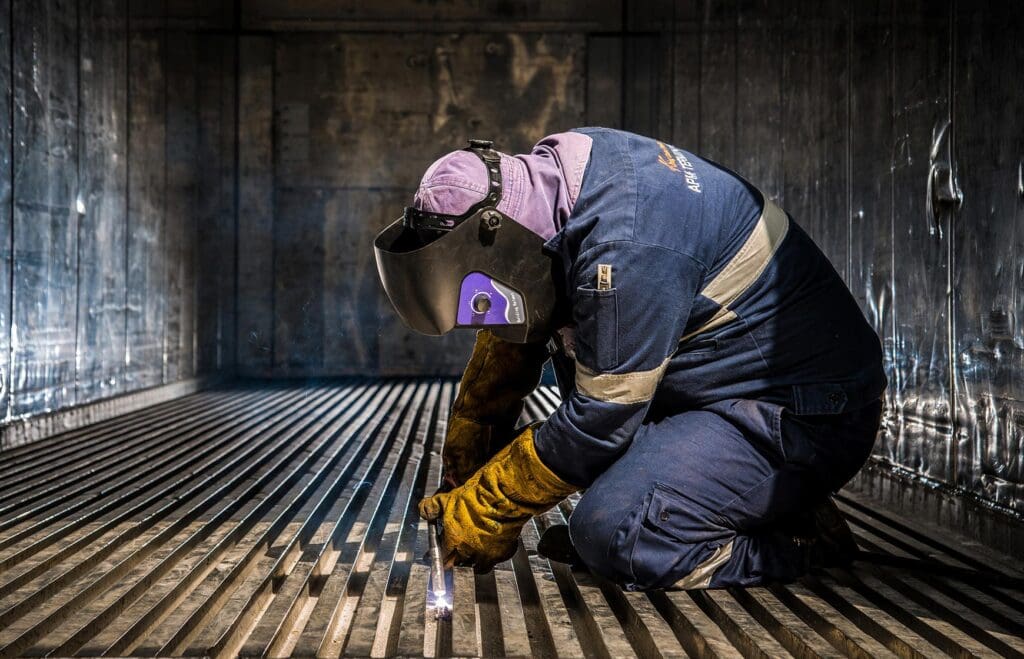
Maintaining a modified shipping container over the long term is crucial to ensure its durability and functionality. Here are key aspects to consider for long-term maintenance:
Rust Prevention and Control
- Regularly inspect for rust, especially in areas where the steel has been cut or welded.
- Keep the container painted with high-quality, rust-resistant paint.
- Repair any scratches or dents to prevent water retention and rust.
Roof Maintenance
- Regularly check and clean the roof to prevent water pooling.
- If you have a flat roof, ensure it has adequate drainage.
- Inspect and maintain any green roofing systems or solar panels if installed.
Insulation and Ventilation
- Regularly check the insulation for any signs of dampness or degradation.
- Ensure ventilation systems are clear and functioning well to prevent condensation, which can lead to rust and mold.
Structural Integrity
- Periodically inspect the container’s structural elements, especially if it has been significantly modified.
- Look for any signs of deformation or unusual stress, particularly around cutouts for windows or doors.
Doors and Windows
- Regularly check the seals around doors and windows to ensure they are watertight.
- Lubricate hinges and locks to keep them working smoothly.
Electrical and Plumbing Systems
- Have regular inspections by a qualified electrician and plumber to ensure systems are safe and up to code.
- Address any issues like leaky faucets or electrical faults promptly to prevent bigger problems.
Interior Maintenance
- Keep the interior clean and dry.
- Repair any interior damage, like chipped paint or damaged floors, to keep the container looking good and functioning well.
Pest Control
- Regularly inspect for signs of pests, especially if the container is in a rural or wooded area.
- l any gaps or holes that could allow pests to enter.
Foundation Care
- If your container is placed on a foundation, ensure that it remains stable and level.
- Check for any signs of shifting or settling, which could affect the container’s alignment and doors’ functionality.
Climate Considerations
- In areas with extreme weather, take additional precautions like extra insulation for cold climates or sunshades in hot climates.
- Regularly check the container after severe weather events.
Ready to purchase a shipping container? Reach out today to get a quote from the best in the industry!
How to Avoid Shipping Container Scams
Shipping Container Scams or as the Better Business Bureau calls them, Sea Can Scams are on the rise, so it is important to do your due diligence when selecting a contractor or shipping container vendor. Here are a few tips on how to avoid shipping container scams:
- Always read reviews– Doing a background check on the contractors and vendors you are looking to use by checking online reviews, testimonials, and feedback from previous customers.
- Be skeptical of extremely low prices– Obtain quotes from multiple suppliers to get an idea of the average cost for your project and it will help you understand the market rate to compare all bids. Be wary of prices significantly lower than market rates, as they might indicate a scam or low-quality product.
- Formal contract, terms & conditions- Ensure all agreements, especially concerning purchases and modifications, are documented in a formal contract. Read the fine print and put everything in writing.
- Learn more– Check out our recent blog to learn more about how to protect yourself before you move forward with the project.
That wraps up our comprehensive guide to customizing your shipping container. We hope it provides you with creative modification ideas, legal and safety considerations, how to find the right contractors and avoid scams. Container Sales Group is a woman owned, shipping container wholesaler since 1998. If we can help you with your shipping container purchase, contact Container Sales Group today by phone at (888) 320-5938 or visit our Get a Quote page to request a customized quote tailored to your specific needs.