Jump to:
Shipping containers have revolutionized global trade, providing a standardized method for transporting goods across the world. One of the critical components of these robust structures is the flooring, designed to withstand heavy loads and harsh conditions. In this blog, we’ll explore what shipping container floors are made of, their construction, and considerations for their use in various applications.
The base of the shipping container flooring consists of (2) two elongated side rails running the length of the container on each side and attached to the back & front rails. Heavy duty steel cross member beams are welded between the long rails every 12 inches to increase the strength of the floor. Shipping container floors are typically comprised of 1-1/8 inch thick marine grade, limited plywood. Each plywood plank is screwed to steel beams on the bottom of the container, which provides the strength and durability the container needs for cargo transport and forklift traffic in and out of the unit. The height of the floor is approximately 6 inches above the ground providing space for ventilation, insulation, and structural supports.
Ready to purchase a shipping container? Reach out today to get a quote from the best in the industry!
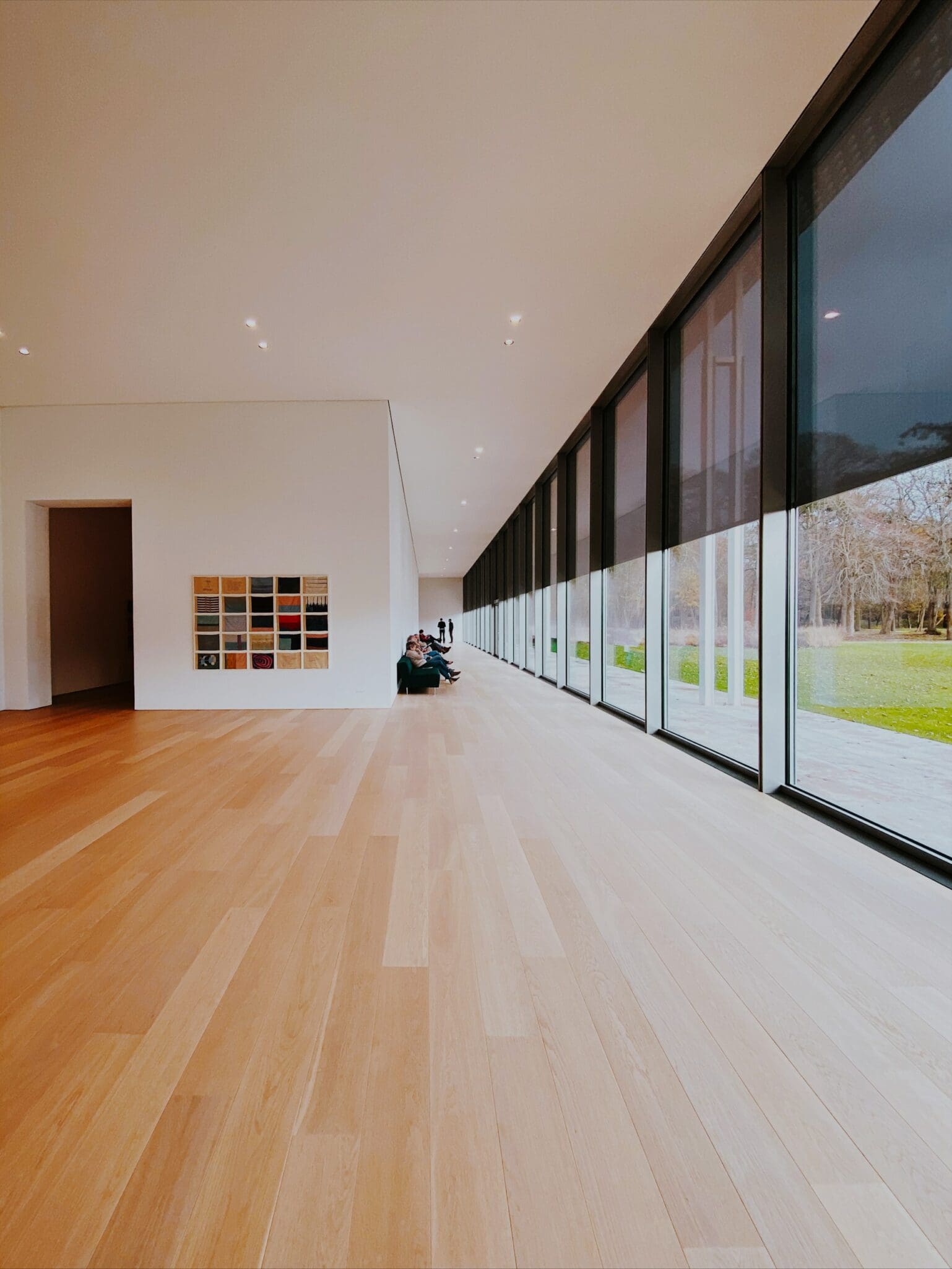
THE BENEFITS AND DRAW BACKS OF SHIPPING CONTAINER FLOORING
MARINE GRADE PLYWOOD ( KERUING AND APITONG)
In the past, shipping container floors consist of plywood crafted from tropical woods like Keruing or Apitong and varies in color from light to dark red brown, or brown to dark brown. These hardwoods are chosen for their high resistance to extreme temperatures, humidity, and the ability to withstand heavy cargo loads. While these woods are durable, they can attract pests. To mitigate this issue, pesticides are often applied to the container floors before cargo transport. It is important to exercise caution to avoid potential toxicity of these chemicals. If you work in shipping containers or use them to build structures, ensuring proper ventilation and following safety guidelines is crucial to prevent exposure to harmful chemicals.
Pro
It can withstand high temperatures, humidity, and the heavy weight placed in the container along with forklift trucks driving in and out.
Con
It attracts pests of all sorts and must be treated with pesticides to protect the goods traveling the world. The odor does dissipate after several years.
BAMBOO WOOD
In recent years, the supply of Keruing and Apitong plywood has decreased, and shipping container manufacturers are now using Bamboo as an alternative. Bamboo is a highly renewable resource that grows much faster than traditional hardwoods and can be harvested in 3-5 years compared to the decades it takes for hardwood trees to mature, making it more of an eco-friendly option. Bamboo is known for its strength and durability. It has a high load-bearing capacity, which makes it suitable for the heavy loads typically placed on container floors. Another benefit of Bamboo is that it is naturally resistant to moisture and pests, reducing the need for chemical treatments that can be harmful to handlers and the environment.
Pro
Environmentally friendly
Durable
Easy to maintain
Pest resistant
Con
Easy to Scratch
Requires special Water Sealants
Not always available in shipping containers.
STEEL
Pro
Protects against moisture, fire, and heavy objects
Pest resistant
Easy to maintain
Recyclable
Con
Not always available in shipping containers
Ready to purchase a shipping container? Reach out today to get a quote from the best in the industry!
Conclusion
Shipping container floors are a crucial component of these versatile structures, designed to withstand heavy loads and harsh conditions. Traditional materials like tropical hardwoods and marine-grade plywood offer durability and strength, while bamboo plywood provides a sustainable and eco-friendly alternative. When using shipping containers for construction, it’s important to consider the potential toxicity of treated wood and take appropriate precautions to ensure a safe and healthy environment.